In an era marked by heightened environmental awareness and the pursuit of sustainable practices, industries around the globe are seeking innovative alternatives to traditional packaging materials. At deSter, we have our own R&D team constantly looking for new materials and new production methods to achieve better efficiency and bring more sustainable products to the Travel and Foodservice markets.
As such, at the deSter Prachinburi plant, the production of wet molded fiber products has commenced. Currently, we have three forming machines in a 1000m2 forming hall. The official start of production was performed during an opening ceremony in June 2023. This is one of the multimillion-dollar investments in the Prachinburi plant which we announced last year.
Understanding Wet Molded Fiber
Wet molded fiber, also known as molded pulp or molded cellulose, is a form of packaging made from a mixture of bagasse (agricultural waste from sugarcane) and water. It is gaining traction as an environmentally friendly substitute for traditional materials such as plastic, foam, or polystyrene. Wet molded fiber has numerous applications, from protective packaging for fragile items like electronics to food trays, egg cartons, beverage carriers, and tableware.
The Manufacturing Process
The production of wet molded fiber products involves several key steps, each contributing to the final product’s strength, shape, and sustainability.
- Raw Material Preparation: Agricultural waste is collected and processed, sorted, and converted into a pulp using water and additives like starch or natural fibers.
- Mold Formation: Pulp is poured into customized molds made from durable materials, and excess water is drained through a mesh screen, leaving a damp fiber mat.
- Pressing and Drying: The fiber mat undergoes pressing to remove water, consolidate fibers, and enhance strength. It is then dried using heat and airflow through natural evaporation or accelerated methods.
- Lamination: For some products with a special application, a thin protective film is applied. For example, to be able to use a product in the oven at high temperatures or withstand moisture from food.
- Finishing and Trimming: Dried molded fiber products are removed from molds, and undergo finishing, which includes trimming excess fibers, surface smoothing, and adding features like fluting or compartments for functionality.
Benefits of Wet Molded Fiber Packaging
Wet molded fiber is made of agricultural waste from sugarcane (or recycled paper), reducing the demand for virgin materials. It is recyclable, biodegradable, and compostable, thus offering a viable alternative to non-biodegradable materials contributing to pollution and landfill waste. Products made of this material contribute to the circular economy and minimize environmental impact.
The flexibility of wet molded fiber enables it to be molded into various shapes and sizes, making it suitable for a wide range of products and applications. It can also be customized to fit the requirements of different customers.
deSter products made in Prachinburi
There are several wet molded fiber products that we currently produce in Thailand for both Travel and Foodservice markets.
RIDGE bowls and lids
The collection of bowls and lids of different sizes is perfect for delivery, takeaway, deli stores & events. They are spill-proof, microwavable, table-ready and can be customized with embossing, stickers, labels, etc.
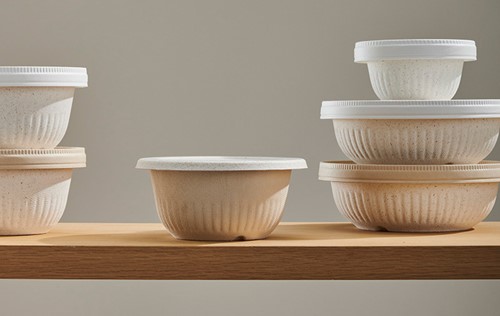
Meat tray for Ikon
This fiber tray produced for our customer Ikon is a sustainable alternative to EPS foam and other plastic trays. It is strong enough to hold even the heaviest food and repels liquid due to the PBAT lamination. It is also “home compostable” certified.
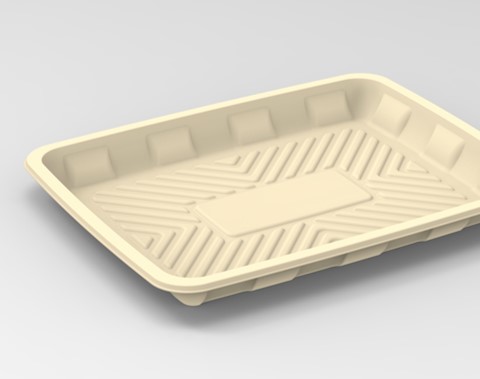
Delta salad bowl (+lid) and casserole
A salad bowl with a lid and a casserole made of wet molded fiber for Delta Airlines’ Economy Class.
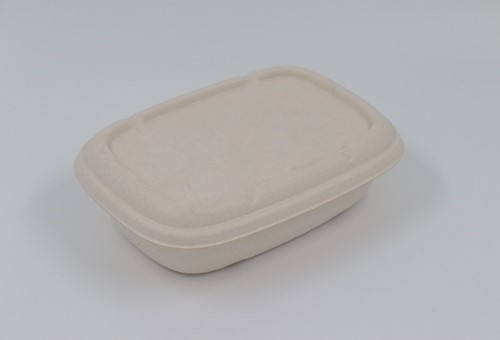